Rethinking Warehousing
With customer demands and warehouse rent at all-time highs, using local space you already own and adopting new tech is key to profitability.
Gone are the days of the Horrea Glabea, the massive Roman warehouse used for storing the public grain supply. While early warehouses were mostly static, today’s warehouses are mostly dynamic, and their primary purpose is for moving products from point A to point B as quickly as possible.
Whether you serve businesses with distribution centers or consumers with fulfillment centers, there’s an expectation of fast delivery times at low or no cost. Storing products, closer to your customers, is the only way to make this happen.
The challenge is that warehouses are often leased and warehouse rent is more expensive than ever. The current demand is outpacing supply in nearly every city. If you’re currently looking to buy a home or recently bought one, this might sound familiar to you.
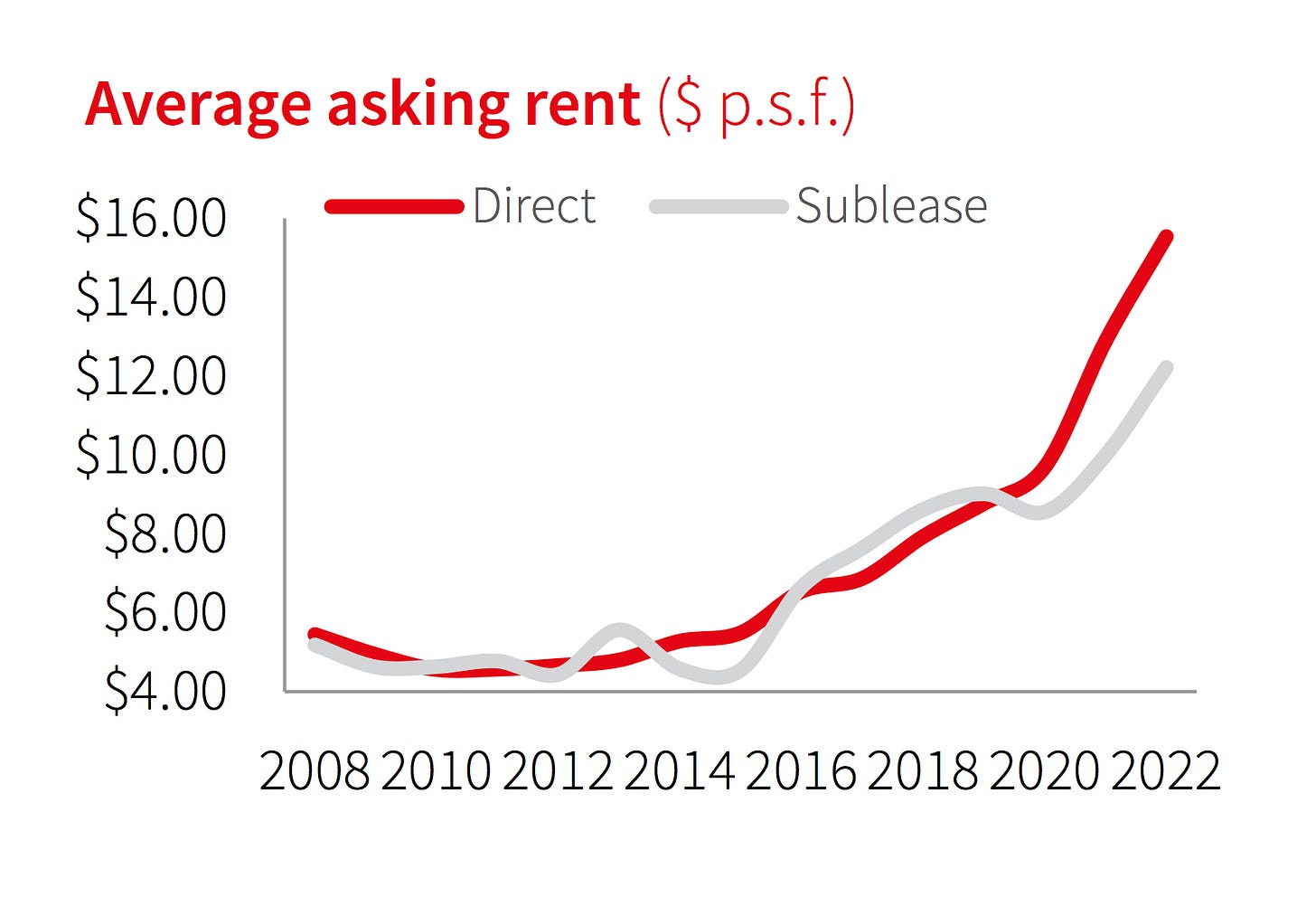
Unlike aspiring homeowners, some companies prefer to rent warehouses from commercial real estate companies instead of building their own. This lets them experiment with placing products in new markets without much risk. But with warehouse rent skyrocketing and the demand for faster delivery, now is a good time to use space you already own if you have it.
If your space is close enough to customers, you can convert it into a high-functioning warehouse with the right technology, people, and partners:
Logistics platform to manage items received, stored, and shipped
Scanning technology on mobile devices for scalable data ingestion across dock to stock and reverse ops
Employees for picking, packing, and preparing items for shipping
Contract with shipping provider or access to on-demand carrier marketplace
Whether you’re a retailer that wants to convert closed stores or back rooms into fulfillment centers or a major distributor that wants to convert an old facility into a distribution center, this is the technology you need on the floor to make any type of warehouse modern and efficient.
If your space is too far away from customers, turning it into a warehouse might not make sense. You’ll have to use the money you save to cover higher transportation costs and your ability to offer omnichannel fulfillment goes away if you planned on using the space as a fulfillment center.
Instead, you can outsource fulfillment or distribution to a third-party logistics provider (3PL) that manages warehousing space closer to your customers. You can also rent out a portion of a warehouse instead of an entire warehouse with warehousing startups like Flexe.
Buying a warehouse is another option. This makes sense for many companies after they hit a certain revenue number and have a firm grasp on where their customers are.
Nike did this when it opened its first distribution center in 1982 after hitting $700 million in revenue. And in 2015 they opened another one in Memphis, Tennessee — one of the largest warehouses in the world. After opening this 2.8 million square-foot distribution center, Nike’s VP of North America Supply Chain Operations said:
“This facility was built to offer greater cost efficiencies, reduce shipping times, and increase service capabilities for our consumers and retail partners.”
The reality is that every major company has a mix of owned, rented, and 3PL-driven warehousing, which often introduces a new challenge — creating a single source of truth for data across all distribution and fulfillment locations.
As the CEO of Flexe recently said on the Logistics of Logistics podcast, warehousing is very fragmented physically and technically as there are thousands of 3PLs and over a hundred different warehouse management systems. I’ve even heard that retailers are thinking of mandating 3PLs to use their preferred tech to reduce this fragmentation.
Tech mandates aside, it’s essential to connect everything together with a homegrown logistics platform, third-party logistics platform, or mix of third-party APIs and integrations that tie into a central platform. Whatever you do, don’t be part of the 50% percent of enterprises that still use pen and paper to manage logistics (the topic of next week’s newsletter).